What Is Remote Maintenance and How It Used in Industry
Remote maintenance is a revolutionary strategy utilized across industries to ensure seamless operations, boost productivity, and reduce outages. By leveraging cutting-edge technology and the power of connectivity, remote maintenance allows professionals to remotely diagnose, troubleshoot, and rectify equipment problems, thereby eradicating the need for on-site visits.
This article explores the concept of remote maintenance, casting light on its practical implementation across various industries and emphasizing its significant cost-effectiveness, efficiency, and overall operational effectiveness and advantages. Without further ado, let’s dive right into it!
- Part 1: What Is Remote Maintenance?
- Part 2: How Does the Remote Maintenance Work?
- Part 3: How Is Remote Maintenance Used in the Industry?
- Part 4: 3 Best Software for Remote Maintenance
- Part 5: The Benefits of Remote Maintenance in the Industry
- Part 6: Trends and Challenges for Remote Maintenance in the Industry
What Is Remote Maintenance?
Remote maintenance is performing maintenance tasks on machines or systems from a remote location, using digital technologies such as sensors, cameras, internet, cloud computing, and artificial intelligence. Remote maintenance can help industries reduce costs, improve efficiency, enhance safety, and overcome geographical barriers.
Different types of remote maintenance monitoring systems can be used to support various maintenance operations. Some of the common types are:
- Remote monitoring and management (RMM) systems – These systems use sensors and software tools to monitor the performance and status of machines or systems from a remote location.
- Remote control systems – These systems allow a remote operator to control a machine or a system from a remote location using a joystick, a keyboard, a mouse, or a voice command.
- Self-guided systems – These systems provide AR instructions to the local technicians through a mobile device or a head-mounted display (HMD). The instructions are usually pre-recorded or generated by an AI system based on the machine model and the maintenance task.
- Expert-guided systems – These systems allow a remote expert to assist a local technician through a live video or audio connection. The expert can see what the technician sees through a camera or an HMD and provide real-time guidance and feedback.
How Does the Remote Maintenance Work?
Remote maintenance operates through a series of interconnected steps allowing technicians to diagnose and resolve equipment issues remotely. The industrial equipment or system has sensors and data collection devices that gather real-time information about its performance, condition, and operating parameters. This data is transmitted securely to a central monitoring system or cloud-based platform.
In the remote location, technicians access the collected data and utilize advanced analytics tools to analyze and interpret the information. They can identify potential faults, deviations, or anomalies that may indicate a problem. Using remote access capabilities, technicians can establish a secure connection to the equipment or system to monitor and control its functions remotely.
How Is Remote Maintenance Used in the Industry?
Remote maintenance is used in various industries to perform maintenance tasks on machines or systems from a remote location by using digital technologies namely, sensors, cameras, the internet, cloud computing, and artificial intelligence.
To understand how is remote maintenance used, here are some of the use cases:
Automotive
Remote maintenance can help the automotive industry to minimize downtime and increase the response time for vehicle issues.
For example, predictive maintenance algorithms can be applied to data gathered through vehicles to identify maintenance issues before they happen.
Airlines
Remote maintenance can help the airline industry track aeroplanes and prevent failures that could affect flight safety and operations.
For example, remote monitoring and management (RMM) systems can use sensors and software tools to monitor the performance and status of aeroplanes and alert the technicians if any problem is detected.
High tech manufacturing
Remote maintenance can help the high-tech manufacturing industry operate optimally and reduce the risk of defects or malfunctions.
For example, self-guided systems can provide AR instructions to local technicians through a mobile device or a head-mounted display (HMD) to perform routine or simple maintenance tasks without needing an expert.
3 Best Software for Remote Maintenance
Considering all the industrial applications of remote maintenance, here are some of the most widely used software that helps specialists carry out operations efficiently:
1TeamViewer
TeamViewer is undoubtedly one of the most well-known corporate remote assistance systems that can be used for remote access and online meetings. There is a free version of TeamViewer available for personal use, and there are commercial versions available for organizations of any type.
The fundamental toolset is included in every version of TeamViewer. However, the most sought-after advanced capabilities, such as bulk deployment, device access log, and multi-connect, are only accessible via the more expensive subscription editions.
Features
- Remote device control
- Secure unattended access
- Chat with customers and colleagues
- Transfer and share files in both directions
- Intuitive touch and control gestures
- Full keyboard functionality (including special keys)
Pros
- Proactive remote IT support
- Maintenance of unattended devices
- Secure and effective
- Intuitive interface
Cons
- Size limit for transferred files
2AnyDesk
AnyDesk is one of the finest remote support tools with a free version for personal use that is limited to one connected device at a time but retains all the fundamental features.
A 256-bit AES encryption algorithm and the precise transfer and screen-sharing features will protect all your traffic from unauthorized access. This solution could be an excellent option if you're searching for customer support for modest enterprises.
Features
- Allows users to share files easily
- Accessible team collaboration
- Remote access/control
- Unattended access
Pros
- Ease of use
- Lightweight and efficient applications
- Multiplatform support for users
Cons
- Requires fast internet connection
3AirDroid Remote Support
AirDroid Remote Support is a robust remote support and remote-control solution that enables you to deliver prompt and trouble-free remote help to your employees, clients, family members, and friends. AirDroid Remote Support may be downloaded from the Google Play Store.
With AirDroid Remote Support for business, technicians and IT professionals can provide remote technical support to users, troubleshoot problems, and perform various tasks on the Android device without physically being present. Besides, it has personal version which provides immediate and efficient remote assistance solutions to elderly, relatives, and friends.
Features
- Real-time screen sharing and file transfer capabilities
- Manage and control unattended and attended Android devices remotely
- Device group management will assist enterprises in enhancing device management
- Hide the screen of the controlled device and display a black screen
- View the status of organization devices and set member role permissions
- A 9-digit code provides a quick and easy connection
Pros
- Secure remote connection
- Professional product services
- Powerful support features
Cons
- Requires subscription to work
The Benefits of Remote Maintenance in the Industry
Adopting remote maintenance in the industry offers a range of significant benefits, revolutionizing traditional maintenance practices and driving operational excellence. Here are some of them:
- Enhanced Operational Efficiency – Remote maintenance allows for real-time monitoring, diagnostics, and issue resolution, enabling proactive maintenance and reducing the occurrence of unexpected breakdowns.
- Cost Savings – Remote maintenance eliminates the need for frequent on-site visits and travel expenses associated with traditional maintenance practices. Technicians can remotely access and diagnose equipment, reducing the time and costs associated with physical inspections.
- Increased Flexibility and Scalability – Remote maintenance allows organizations to manage and maintain equipment or systems across different locations and facilities from a centralized remote location.
Trends and Challenges for Remote Maintenance in the Industry
As remote maintenance continues to evolve, several trends and challenges are shaping its implementation across various industries. Understanding these trends and overcoming the associated challenges is essential for maximizing the benefits of remote maintenance.
Trends
Increased Adoption of IoT – IoT devices and connectivity integration is witnessing rapid growth in remote maintenance. IoT enables real-time monitoring, predictive analytics, and automation, empowering technicians to monitor and manage equipment more efficiently remotely.
Advancements in Artificial Intelligence – AI-driven technologies, such as machine learning and predictive analytics, are revolutionizing remote maintenance. These technologies enhance fault prediction, optimize maintenance schedules, and enable more accurate diagnostics, improving overall operational efficiency.
Remote Assistance through Augmented Reality – Adopting augmented reality (AR) is becoming prevalent in remote maintenance. AR-based assistance systems provide real-time guidance to on-site technicians, allowing remote experts to visualize and guide repair processes, leading to quicker problem resolution and reduced downtime.
Challenges
Security and Data Privacy – With remote maintenance relying on data transmission and remote access, ensuring robust cybersecurity measures is crucial. Protecting sensitive equipment and data from potential cyber threats, unauthorized access, and data breaches poses a significant challenge that requires continuous vigilance and proactive security measures.
Skill Requirements and Training – Remote maintenance demands skilled technicians proficient in handling advanced technologies and software tools. Upskilling the workforce and providing comprehensive training to leverage remote maintenance systems effectively can be challenging for organizations, requiring investment in training programs and resources.
Connectivity and Infrastructure – Remote maintenance heavily relies on stable and reliable connectivity, which can be challenging in remote or geographically dispersed locations. Ensuring adequate connectivity infrastructure, such as high-speed internet access and network reliability, is necessary to support real-time monitoring and seamless remote maintenance operations.
Hottest Questions Related to Remote Maintenance
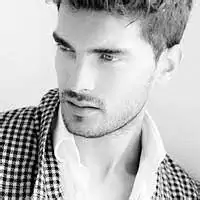
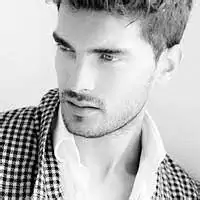
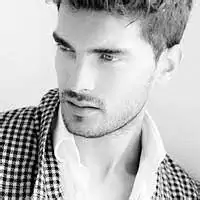
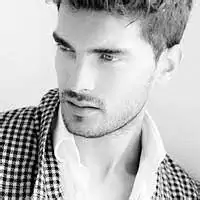
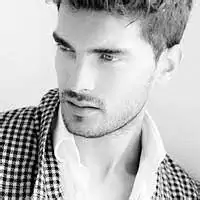
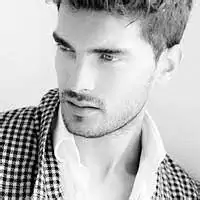

Leave a Reply.